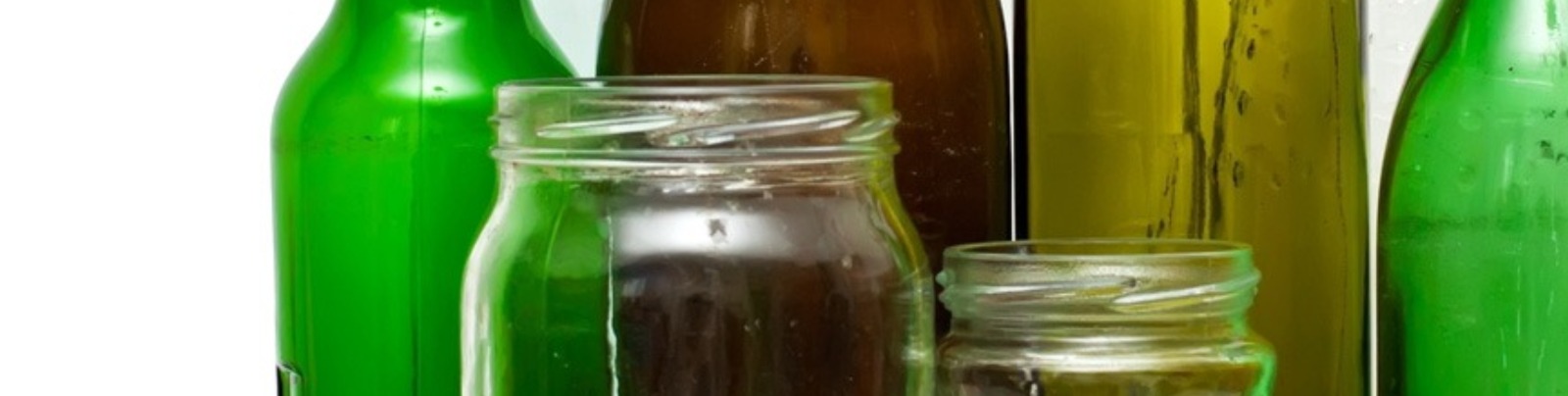
Glass - Recycling Process
How is glass recycled?
Recycling glass is a simple but hugely beneficial process. Below are twelve steps to recycling this complex material. The images also demonstrate the complete recycling loop as glass can be recycled repeatedly.
- Raw materials
- Glass container making
- Transportation to retailers
- Use at home
- Dumping glass
- Glass collection
- Commercial collection
- Removing contaminants
- Container making
- Alternative uses
- Exporting glass
- Closing the loop
Raw materials
There are four main ingredients:
- Cullet (recycled glass)
- Sand
- Soda ash
- Limestone
Even though basic ingredients are used in vast quantities, accurate weighing and mixing to achieve precise proportions is critical. This procedure is carried out electronically in the batch house, which supplies the mix to the furnace.
A typical furnace within the glass container industry will operate 24 hours a day, 365 days of the year producing around 300 tonnes of glass a day! This production of glass is continuous for the furnaces' lifetime of approximately 10 years.
Up to 90% recycled glass is mixed with raw materials and fed into the furnace where the recycled glass remelts and becomes pure and pristine again.
Glass container making
The glass is cut into "gobs" and these individual pieces are fired down into the forming machine. Within seconds, the glass is pressed and blown into shape within a mould and emerges as a glass bottle or jar!
Each container is subjected to a rigorous series of quality checks.
A typical quality regime will include:
- Automatic online, wall thickness inspection
- Squeeze testing
- Sealing surface inspection
- Side wall scanning
- Base scanning
At intervals, a sample of the containers being produced is taken aside for dimensional checks, capacity checks and pressure testing. If any problems are found in production since the last check, it is set aside for further inspection. This procedure is followed until the production again passes the tests.
The data from online and offline quality checks is fed continuously back to the 'hot-end' forming machine operators who can then make adjustments to remove the problem at source.
Each container has a series of dots moulded into the insweep, which create a coded number when read by the online inspection machines. This quickly highlights any bottle faults being seen and faults in the mould, which is creating it.
Transportation to retailers
The bottles and jars are filled with food and drinks and taken to retailers such as supermarkets where they are sold to consumers.
In addition, UK retailers and brand owners import over 1 million tonnes of empty and filled glass packaging each year, meaning that the total UK waste stream for glass packaging in 2012 was approximately 2,399,000 tonnes.
Many bottles of beer, spirits and soft drinks are taken direct to retailers such as pubs, restaurants and nightclubs where they are sold to consumers.
Use at home
The rest of the glass is taken home by consumers who eat or drink the products inside the bottles or jars.
They then make a crucial decision, do they throw it in the bin, put it in their kerbside collection container or take it to the recycling bank?
If they throw it away it will go to landfill where it will stay forever, never breaking down. If they take it to be recycled, the whole cycle begins again and glass can go on being recycled again and again - forever.